What You Need to Know About Tracks, Pads, and Buffers (Interview With John Ibrahim)
There is nothing worse than a machine going down when you’re under the pump. If you don’t have the right parts available, downtime quickly becomes expensive and frustrating.
For our customers, time is money. And when it comes to quality, TrackPads Australia is our number-one choice for premium rubber products. We should know… we put our own name behind it.
We recently sat down with John Ibrahim, our National Aftersales Manager to speak to him about what makes TrackPads Australia different from other brands.

We also picked his brain to see what tips he had for extending the product life span and some of the biggest mistakes he sees people making with installing and caring for their parts.
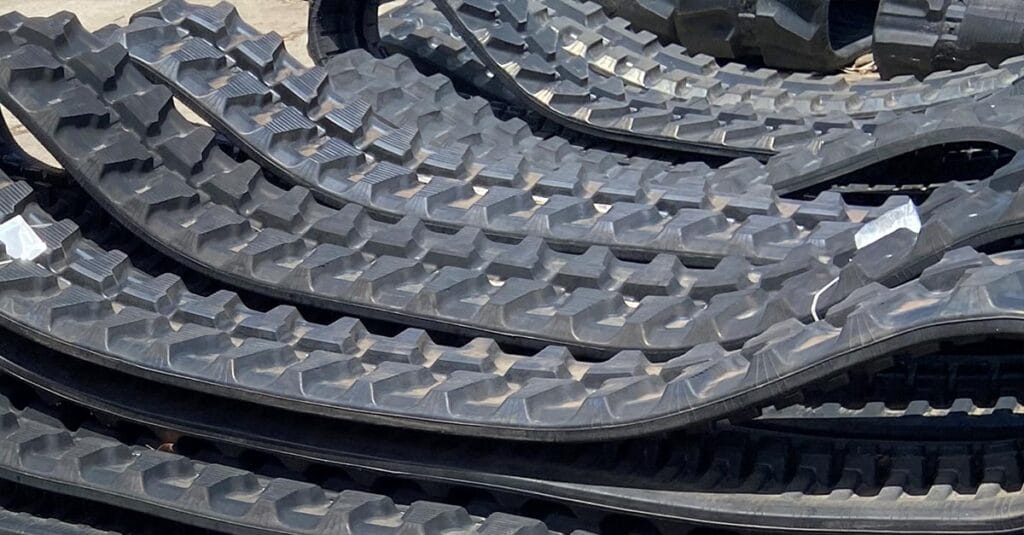
The TrackPads Australia interview with John Ibrahim
Our customers know and rely on John to help them get what they need — even if it means jumping in the car himself. With 30 years of experience at Conplant, it is safe to say that John knows our parts inside and out, and he understands the pressure of needing parts in a hurry. Now let’s hear from the man himself…
What is important for customers to understand when searching for tracks, pads, and buffers online?
“Buying parts online can be confusing, even if you know what you are looking for. Getting the right size, shape and brand is a headache, and if you find the part you need, delivery becomes the next headache. When buying tracks, pads and buffers online, weight is key. The heavier the item, the more of it there is.
Our team knows the task is hard, so we’ve created some handy buying guides to make it easier to get what you need online.”
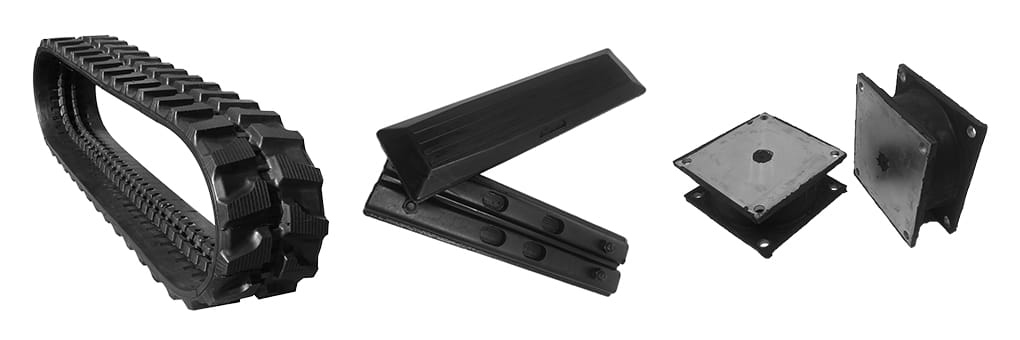
What makes TrackPads Australia different from other options in the market?
“They provide premium quality products from rubber that is specially formulated to suit the harshest Australian conditions. Their products have the right amount of flex and hardness, which is key to performance and product longevity.
The rubber buffers, for example, are guaranteed not to peel from the rubber, and they don’t split. There is no question how much of a difference that can make when you are in the middle of a big job that can’t afford any downtime.
They also have an impressive range of compatible track pads for all of the biggest brands and an extensive parts inventory available nationwide.”
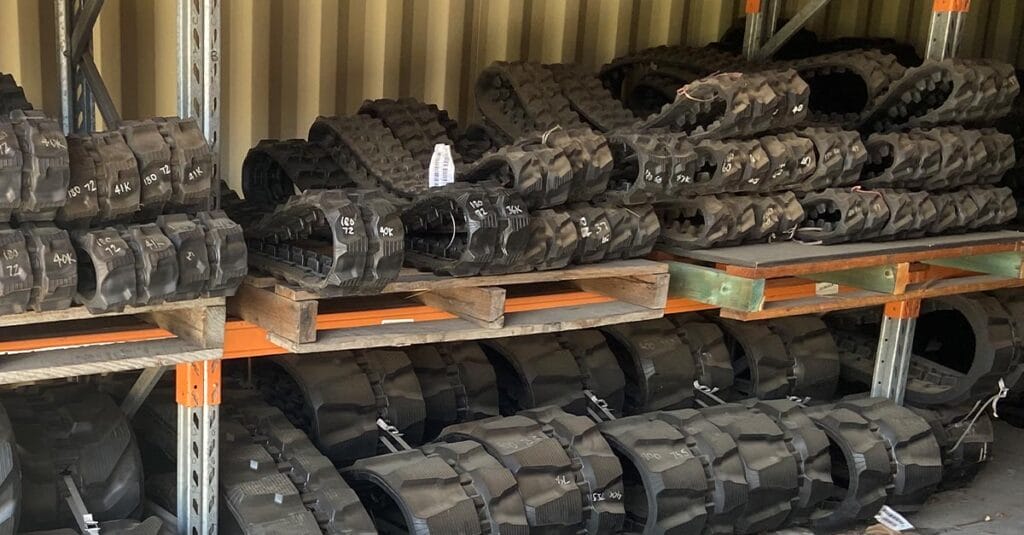
What are the consequences of using cheap and inferior tracks, pads, and buffers?
“As with everything, you get what you pay for. Buying cheap often means expensive when it comes to downtime and unforeseen, costly mechanical damage caused by high vibration or loose tracks.
Parts that can’t handle the conditions end up deteriorating, splitting, and ultimately bringing projects to a grinding halt.”
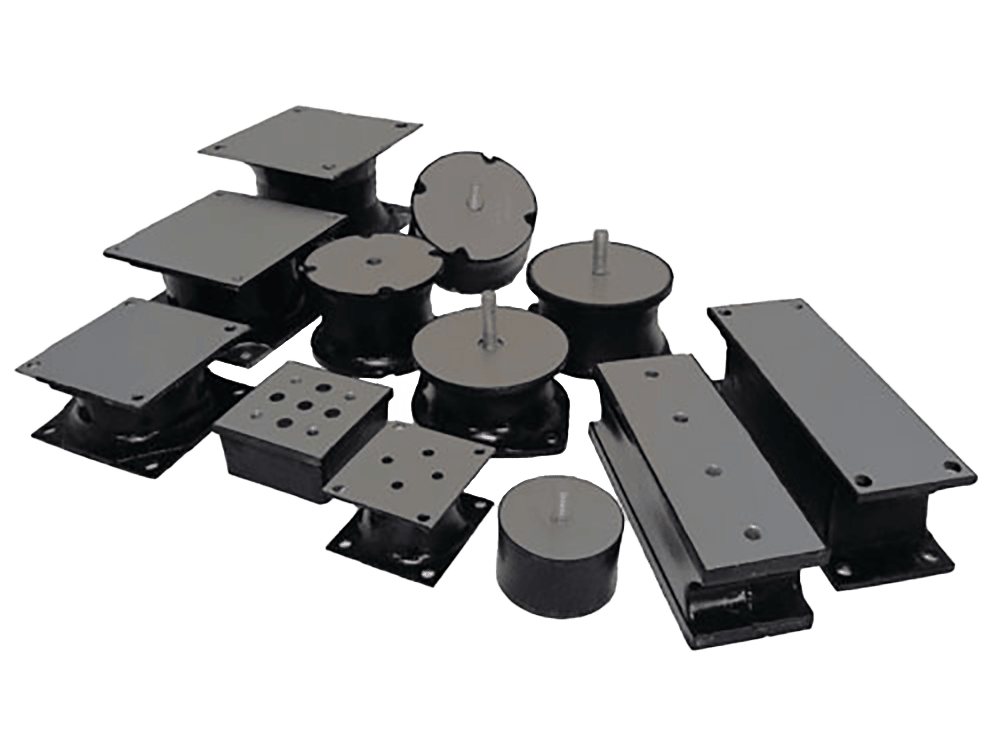
If you buy inferior products, you buy twice!
It’s as simple as that. Not only does it have a direct financial impact on your business from down time and having to cough up for a second set of tracks in the near future, but it can do unrepairable reputational damage to you and your business if you can’t meet your customers project deadlines, which impacts your current job and the likelihood of repeat business.
What is the biggest mistake you see customers making when it comes to installing and/or caring for their tracks and pads?
“Not keeping them adjusted and clean, and not replacing worn idlers, rollers or gears when needed. Keeping on top of regular maintenance is crucial to keeping machines running smoothly.
Not even the best quality parts on the market can circumvent the need for regular cleaning and adjustments. Worn parts that need to be replaced but are left running too long end up impacting other parts along the way.”
Can you share any tips for extending the lifespan of the tracks and pads you sell?
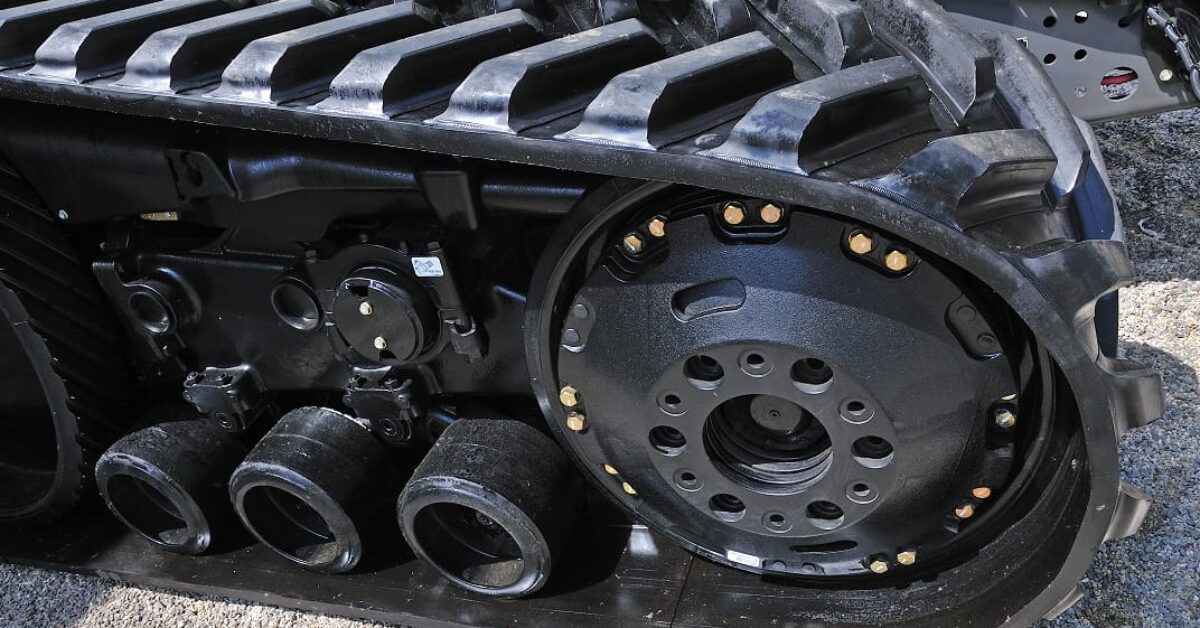
“Be gentle on them; no sharp turning or screwing. Keep them adjusted correctly and, as always, keep up with scheduled maintenance and cleaning.”
Want to chat to one of our Conplant’s parts experts?
Reach out to our team today to chat about:
Keep your machines running and your projects moving forward with TrackPads Australia at Conplant!
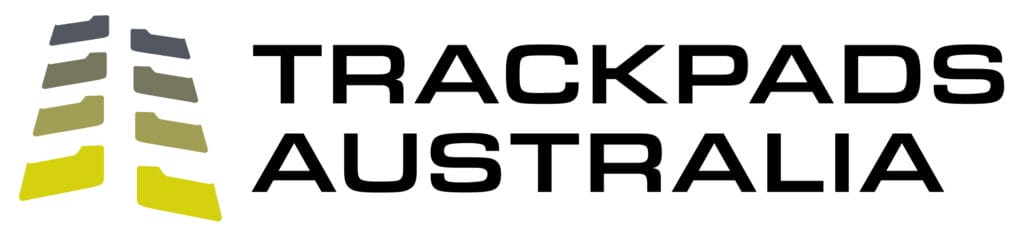