Air Filters for Compaction and Construction Equipment (Everything You Need to Know)
Are you experiencing a decline in the performance of your compaction equipment? Are you hearing strange noises or noticing dirt and dust in the engine? These are common issues that occur when the filters and fluids in diesel-powered equipment are not properly maintained.
At Conplant, we have decades of experience in dealing with all types of mistakes related to construction equipment parts, filters, and oils. And predictably, one of the most common reasons for construction equipment failure is the incorrect treatment of filters.
In this blog, we’ll explore the importance of air filters in protecting your compaction equipment and maintaining the performance and safety of your machines on the job site.
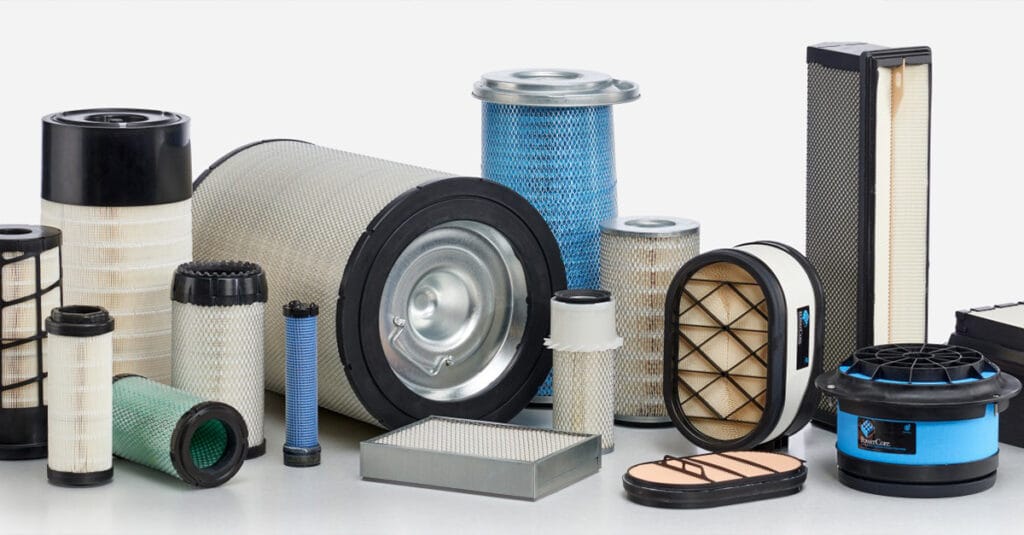
Understanding the different types of engine air filters for compaction equipment
Selecting the right engine air filter for your compaction equipment is vital for maintaining its optimal condition. There are different types available — designed for different applications and made of various materials. Making the best choice will help to extend the life of your equipment and reduce the risks of unplanned breakdowns.
The main types of air filters on a compaction roller are:
- Fuel filters
- Hydraulic filters
- Oil filters
- And of course, air filters
An engine air filter is a cartridge containing very fine media and many small holes for the air to pass through. Selecting the right materials depends on your specific application, environment and also the manufacturer’s recommendations. There are several common types, including:
- Paper
- Gauze
- Foam
- Fibreglass
- Polyester
- And pleated air filters
Their primary function is to make sure the air being forced into your engine is clean (free from dust and other particles). Air is a critical component of the combustion process and maintaining clean air is crucial for keeping your compaction equipment operational.
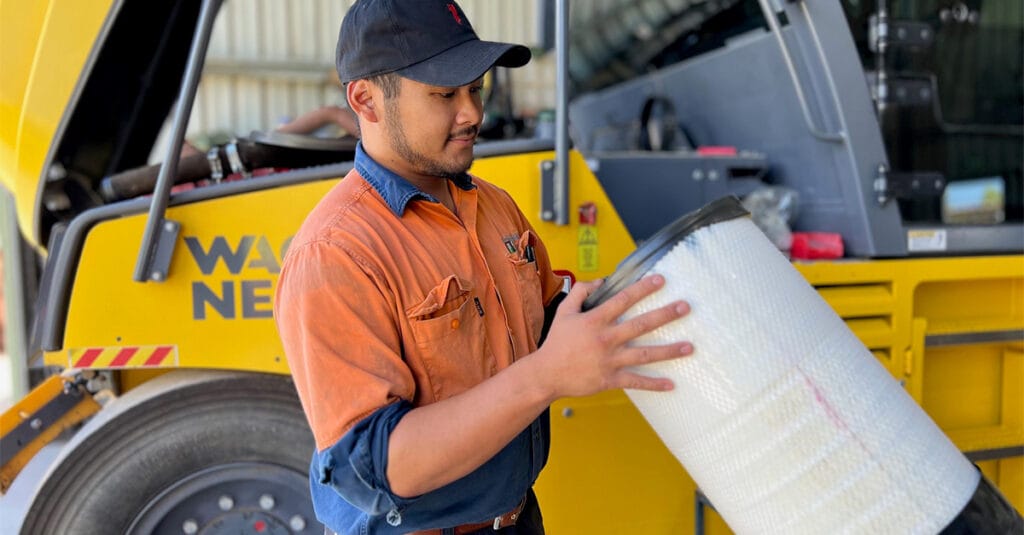
There are two essential factors to consider when it comes to engine air filters:
- Selecting the right filter for your compaction equipment
- Ensuring it remains effective for as long as possible
To keep your equipment in the best working condition, pre and post-operation checks on your filters are a must. This allows you to identify any issues with your air filters before getting stuck into your next project. These checks mean you can avoid costly delays and disruptions — which could be the difference between finishing the project on time or not.
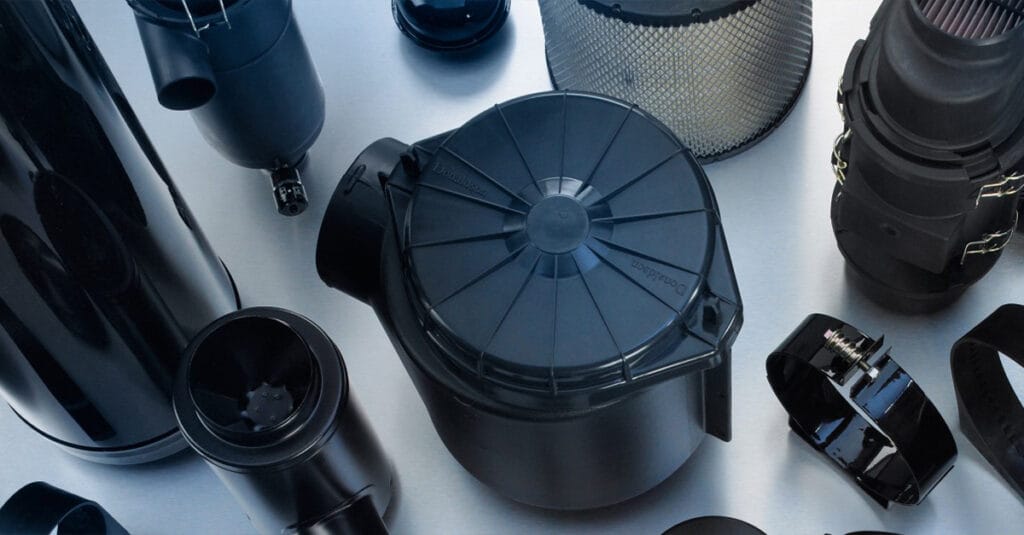
The heavy consequences of ignoring damaged or faulty air filters
Failing to address damaged or faulty air filters can lead to serious consequences for your equipment, warranty, and your bottom line. Let’s have a look at some of the hidden dangers and how to avoid them.
Think of the air intake system on your compaction roller as the set of lungs giving it life. A damaged or faulty air filter will result in the engine taking in dirty air, causing damage to turbochargers and internal engine parts (including valves, pistons, and cylinder walls). Other (less common) consequences include excessive oil and fuel consumption and poor engine performance, eventually leading to engine failure.
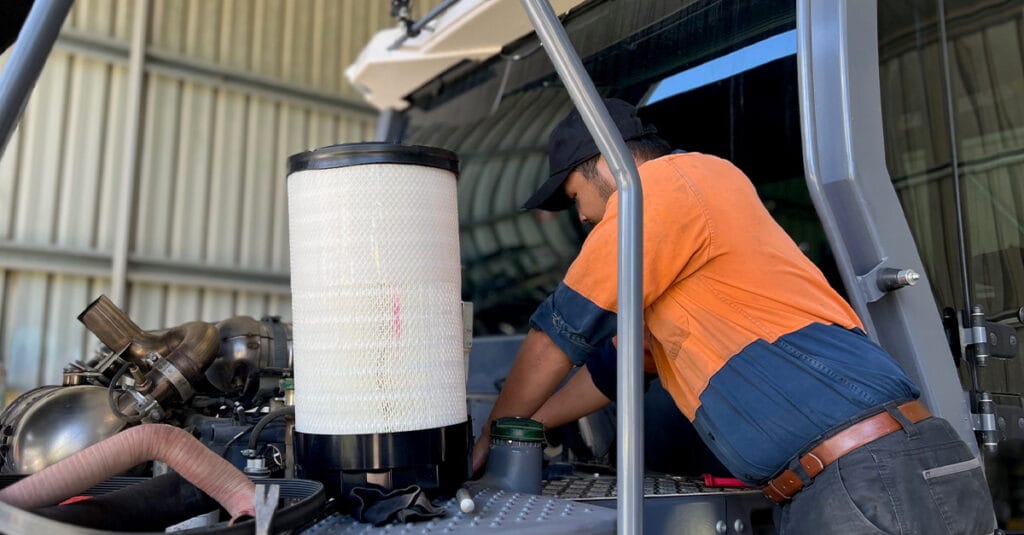
How to avoid disaster with your air filters
We recommend you check your service manual but as a rule of thumb, it is ideal to replace your filters at 1,000-hour intervals.
Alternatively, whenever you think they need to be replaced — such as:
- When working in harsh environments, the filter may become clogged with dirt or other contaminants
- Or if you notice any signs of deterioration — such as a decrease in airflow, engine performance issues, or increase fuel consumption
To avoid costly delays in your projects, we recommend you always keep replacement air filters on hand. Even with correct care and maintenance, you never know when you might need to fit your machine with a fresh filter.
Remember, the ultimate consequence of damaged or faulty air filters can be costly repairs, reduced equipment lifespan, and unexpected breakdowns resulting in less productivity on site.
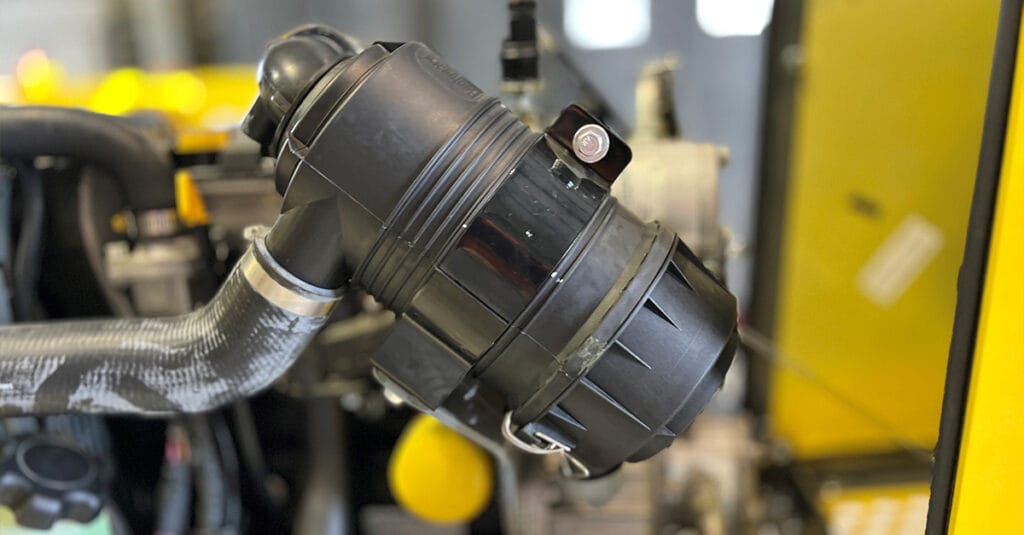
A closer look at primary and secondary air filters
Most compaction roller air cleaning systems have two filters. The large filter is the primary air filter that does most of the hard work — removing contaminants coming from the air intake system. The second smaller filter is fitted inside the primary filter and is known (appropriately) as a secondary or inner filter. This is also referred to as the safety filter — which accurately describes what it does.
1 - Caring for your primary air filters
With a little care and attention, you can ensure that your filters keep doing their job longer. The first two things you want to check:
- Make sure there are no splits, rips and holes, or damaged seals
- Make sure that the air filter is securely fastened in place
We suggest you check once and then check again — because the number of dusted engines we’ve seen over the years from a filter not being fitted correctly would shock you.
Whilst it is possible to clean your air filters with high-pressure air — we strongly suggest you do not do this. Why? As you blow air out of the filter, dust particles go everywhere and regardless of how careful you are, there is a good chance that dust could remain on the inside of the filter and make its way inside the engine.
Air filters should only be cleaned by a professional company trained in the art of proper care. Remember, your results will only be as good as the systems and people responsible for the cleaning.
What not to do with your engine air cleaner filter?
- Never strike the air filter with a tool
- Never disassemble your element to clean it
- Never hit the air filter against the ground or a table to release dust
Never scrape any contaminant from the filter surface, or filter media
2 - Caring for your safety air filter
The safety filter is designed as a backup during operation in case of filter or fitment failure. It can be either pleated or a slim line design — often made from a different media to the primary filter. The safety filter protects the engine during servicing. Here are some tips to keep in mind:
- Never run the engine with only the safety air filter
- It is recommended to replace the safety filter with every third primary filter change unless there has been a failure
- Never clean a safety filter
- Fitment of a safety filter is proven to be the most effective method for providing added protection to your engine
- Unnecessary handling of air filters can cause unwanted damage
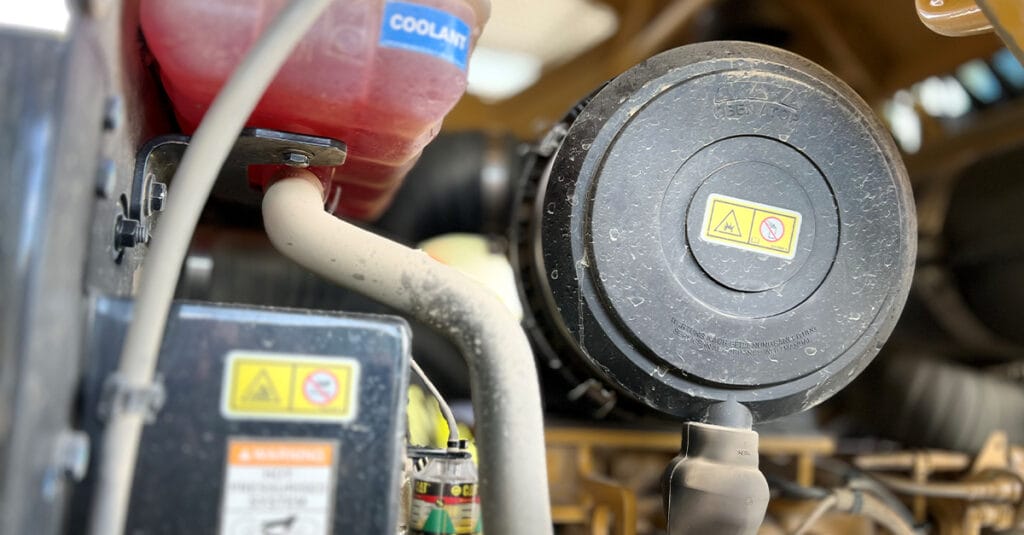
Need new air filters?
Well, you’re in the right place… have a chat with the experts behind the parts counter at your nearest Conplant branch! We’ve got filters, oils and lubricants for all of your compaction and construction equipment — including hydraulic oil, coolant and gear oils.
We know finding the right filters or oils can be tricky… but even if your part numbers have worn away or you don’t know what you need — we’ll be able to sort you out. Our experienced team will take a look and give you a few options to get you back up and running. We have all the big brands, including Wacker Neuson and Deutz. Get in touch with us today!