Every successful construction project must start with stable ground, which means proper compaction. Luckily, we know some compaction experts 😊 In this guide, we explore the critical role compactors for soil play in creating safe, long-lasting structures and how to choose the right method and equipment for your job.
Contents:
The Importance of Soil Compaction in Construction Projects
Understanding Soil Compaction and Its Impact on Stability
Different Types of Soil and Their Compaction Requirements
Top Soil Compaction Techniques and When to Use Them
Risks of Poor Soil Compaction in Construction
Best Practices for Achieving Effective Soil Compaction
Choosing the Right Compaction Equipment for the Job
Soil Compaction at Different Stages of Construction
How to Select the Right Compaction Equipment
Why Single Drum Rollers Are Central to Site Stability
Case Study: Bindoon North Highway Upgrade
The Importance of Soil Compaction in Construction Projects
Proper soil compaction ensures stability and durability in construction projects. When soil is compacted correctly, it provides a solid base that prevents settling, shifting, and structural failure. Well-compacted soil improves load-bearing capacity, reduces permeability, helps control erosion, and enhances resistance to water infiltration and freeze-thaw cycles. It also contributes to more efficient construction timelines by minimising rework and equipment stress, setting a reliable foundation for every subsequent project phase.
Inadequate compaction leads to unstable ground conditions, increasing maintenance costs and the likelihood of expensive repairs. Soil compaction is essential for long-term structural integrity, whether for roads, buildings, or bridges. Understanding how this process works – and the factors that influence its success – is key to ensuring construction quality from the ground up.
Compaction is the backbone of any successful construction project, providing a solid foundation for every layer that follows. Choosing the right equipment isn’t just about size or power – it’s about matching the roller to the material behaviour, moisture content, and lift thickness to achieve target density across varying soil profiles to meet design specifications. With so many variables on site, operators and supervisors need equipment they can rely on to perform consistently, especially on large-scale infrastructure jobs where productivity and accuracy are everything. Uniform compaction not only enhances long-term durability but also ensures that each layer can do its job properly.
Dwayne Rosie
Understanding Soil Compaction and Its Impact on Stability
Soil compaction is the process of increasing soil density by reducing air gaps between particles. This improves the soil’s strength and stability, preventing water infiltration that could lead to erosion or shifting. Several factors influence soil compaction, including:
- Moisture Content: The right amount of water helps particles bind together, while excessive moisture leads to weak compaction.
- Soil Type: Different soils compact differently based on particle size and composition.
- Compaction Method: The choice of compaction technique determines effectiveness.
Understanding these factors helps in selecting the right approach for each project – and it all starts with knowing the soil you’re working with – and choosing the right compactors for soil to handle it effectively.
Different Types of Soil and Their Compaction Requirements
Different soil types respond differently to compaction, so understanding their properties is key to choosing the right method for each project.
Clay
- Holds moisture well but can shrink and expand.
- Requires heavy compaction effort and optimal moisture control.
Sand
- Drains quickly and compacts easily with vibration.
- Best compacted using vibratory rollers.
Silt
- Can retain water, leading to poor compaction.
- Requires aeration and gradual moisture reduction before compaction.
Identifying soil type is critical in selecting the most effective compaction technique, as it directly informs which roller or method will deliver the best results in the next stage of your compaction plan.
Top Soil Compaction Techniques and When to Use Them
Each soil compaction technique has specific strengths, and knowing when to use them depends on the soil type, project size, and load requirements.
- Static Compaction: Uses heavy rollers to apply pressure. best for cohesive soils like clay and asphalt, where a kneading action effectively densifies the material. It’s also useful for proof rolling, finishing work, and in situations where vibration is undesirable or less effective.
- Vibratory Compaction: Uses rapid vibrations to reduce air gaps in soil. Ideal for sandy and non-cohesive soils.
- Impact Compaction: Uses repeated force to compress soil layers. Effective for cohesive soils like clay.
- Pneumatic Compaction: Uses rubber-tired rollers to achieve uniform density. best suited for sealing surfaces and compacting softer materials like asphalt, granular soils (sands and gravels), and even some cohesive soils with lower plasticity.
Choosing the right compaction method depends on soil composition and project requirements – and it’s just as important to understand the risks of getting it wrong.
Risks of Poor Soil Compaction in Construction
Failing to compact soil properly can lead to several issues, many of which create long-term challenges for the structure and the people maintaining it:
- Foundation Failure: Unstable ground causes cracks, uneven settling, and structural deformation. This may not be noticeable right away but can escalate into serious safety and cost concerns.
- Increased Maintenance Costs: Surfaces like roads, pavements, or slabs may develop uneven wear, potholes, or shifting that requires constant repair.
- Water Damage & Erosion: Poorly compacted soil has more voids, allowing water to enter and weaken the soil structure. Over time, this can lead to erosion or even washouts.
- Reduced Load-Bearing Capacity: Soil that isn’t compacted to the required density cannot effectively support weight from above. This impacts everything from machinery stability during construction to the durability of finished structures.
- Delayed Project Timelines: If compaction is insufficient, rework is often needed, slowing down progress and driving up costs.
Ensuring proper compaction minimises these risks and enhances construction longevity—something every builder aims for as the project moves into more complex phases like foundation pouring, structural framing, or surface finishing.
Best Practices for Achieving Effective Soil Compaction
Achieving adequate compaction requires more than running heavy machinery over the ground. It involves a strategic approach to ensure every layer of soil is prepared, placed, and compacted under the right conditions. To optimise soil compaction:
- Analyse Soil Conditions: Test for moisture content and classification.
- Choose the Right Equipment: Match machinery to soil type and compaction needs.
- Compact in Layers: Apply even pressure in multiple thin layers rather than thick ones.
- Monitor Moisture Levels: Maintain ideal moisture content to prevent overcompaction or weak bonding.
- Conduct Density Testing: Use field tests to confirm compaction meets project specifications.
Following these practices ensures reliable soil stability across all construction phases – especially when combined with the right compactors for soil.
Choosing the Right Compaction Equipment for the Job
When we talk to contractors, the big challenge isn’t finding equipment—it’s finding confidence in how that equipment will perform under real site conditions. That’s why we focus so much on reliability, service, and giving crews the tools they know they can trust, shift after shift.
Liam Brosnan
Matching your equipment to the job isn’t just good practice – it’s essential for achieving the right compaction outcomes. With different soil types, site constraints, and project demands, choosing the right machine can make or break your timeline and long-term stability. Here’s a breakdown of common compaction equipment and where each one performs best:
- Plate Compactors: Best for small areas and granular soils.
- Padfoot Rollers: Designed for compacting cohesive soils like clay.
- Vibratory Rollers: Ideal for sand and gravel, using vibrations to settle particles.
- Pneumatic Rollers: Suitable for roads and pavement projects, using rubber tyres to achieve uniform density.
Selecting the right equipment is key to achieving consistent compaction. For more information, read our blog on choosing the right compactors for soil.
Soil Compaction at Different Stages of Construction
Soil compaction plays a critical role at multiple stages of construction, from initial site prep to final grading, and its application must be adjusted as the project progresses.
- Site Preparation: Ensures stable ground before foundation work begins.
- Foundation Laying: Prevents settlement issues and improves load distribution.
- Road Construction: Reduces pothole formation and extends road lifespan.
- Landscaping & Earthworks: Provides a stable base for retaining walls and drainage systems.
Regular compaction checks throughout construction maintain stability and prevent future issues.
How to Select the Right Compaction Equipment
When selecting compaction equipment, it’s important to consider more than just the size or brand. Here are four key factors that determine the most effective machine for your project:
- Soil Type: Clay, sand, and silt respond differently to compaction. Matching your equipment to the specific soil type ensures better results.
- Project Size and Scope: Large-scale roadworks or infrastructure jobs may require heavy-duty machines, while smaller landscaping jobs might benefit from more compact or walk-behind equipment.
- Site Access and Conditions: Confined spaces, steep grades, or wet environments may limit your options, so equipment agility and design must be considered.
- Moisture Content: Equipment performance can vary depending on soil moisture levels. Machines with adjustable settings can help fine-tune the compaction process.
Why Single Drum Rollers Are Central to Site Stability
When establishing the foundation of every construction project, single drum rollers – smooth and Padfoot – are the go-to machines for performance and consistency. Smooth drum rollers are ideal for granular soils and large-scale road construction, while Padfoot rollers shine for cohesive materials like clay. Conplant offers rollers for different compaction needs across infrastructure, civil works, and site prep projects.
Below is a quick guide to help you choose the right equipment:
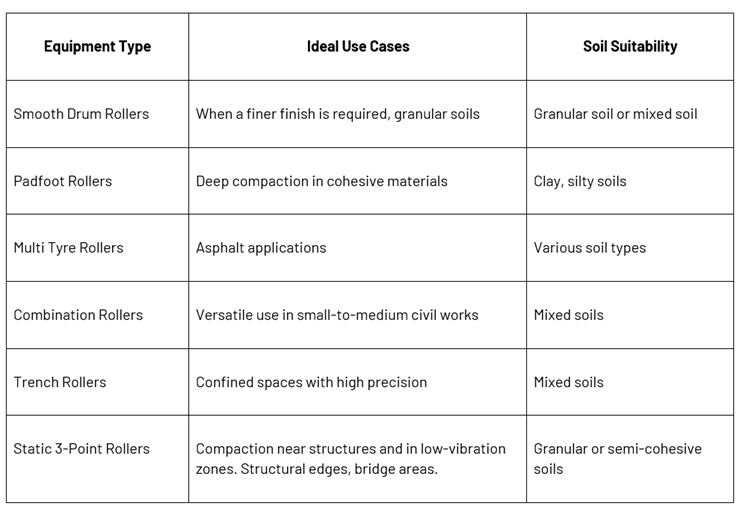
View the full fleet and request a hire here.
Case Study: Bindoon North Highway Upgrade
Between March 2023 and May 2024, Conplant supported Garli on the Bindoon North highway upgrade in Western Australia. This large-scale infrastructure project involved widening and realigning a key section of the Great Northern Highway.
Conplant supplied a fleet of up to 10 rollers in use at one time, including smooth drum and Padfoot machines, to help compact more than 210,000m³ of earthworks and 230,000m² of pavement. The result? Consistent compaction quality, reduced rework, and reliable performance under pressure.
Read more about the project here.
Why Proper Soil Compaction Matters
Soil compaction is more than just a checklist item on your site prep – it’s a defining factor in how well your entire project performs. It’s the step that sets the tone for everything that follows, from foundations to final finishes. Using the right compactors for soil, techniques, and quality control measures will result in structures that stand the test of time.
Frequently Asked Questions (FAQs)
Soil compaction in construction is crucial for increasing soil density and stability, which enhances its load-bearing capacity and reduces settlement. This improved soil strength provides a stable foundation for structures like buildings and roads, preventing future issues like cracking and uneven surfaces.
The main purpose of soil compaction is to increase the soil’s density by reducing air voids between particles, leading to greater strength and stability. This densification improves the soil’s ability to support loads and minimizes settlement in construction projects.
The purpose of the compaction process is to increase the density of soil by reducing the volume of air voids between soil particles. This densification strengthens the soil, improves its stability, and enhances its ability to support construction loads, ultimately minimizing settlement and increasing the longevity of structures.
Soil compaction before pouring a concrete slab is essential to create a stable and level base that can support the weight of the slab and any future loads. Proper compaction minimizes soil settlement, which could otherwise lead to cracking and structural issues in the concrete slab over time.
There are several methods to test if soil is properly compacted, including field density tests like the sand cone method and nuclear density gauge, which compare in-place density to laboratory maximums. Intelligent compaction (IC) technology, such as systems offered by Völkel, provides real-time monitoring of compaction using specialised rollers equipped with sensors and GPS. These systems measure parameters like material stiffness and pass counts, offering continuous data and color-coded maps to ensure uniform and adequate compaction across the entire site, often reducing the need for traditional spot tests.
The ideal moisture content for compaction, often referred to as the optimum moisture content (OMC), is the specific amount of water in the soil that allows it to achieve its maximum dry density for a given compaction effort. At this moisture level, water acts as a lubricant between soil particles, facilitating their movement and closer arrangement to expel air voids effectively. Determining the OMC is crucial as too little moisture leads to stiff soil resisting compaction, while too much water fills void spaces and prevents dense packing of soil solids.
Yes, soil can be over-compacted. While compaction aims to increase density and stability, excessive force can break down soil structure, reduce pore space too much, and impede root growth, water infiltration, and air circulation. Over-compaction can lead to a hard, almost impermeable layer that is actually detrimental to plant health and overall soil function.
For compacting clay soil, equipment that applies impact force and kneading action is most effective. Sheepsfoot rollers and padfoot rollers are specifically designed with protruding feet that penetrate and manipulate the cohesive clay particles, promoting deep compaction. Upright Rammers, aka Tamping Rammers – jumping jacks, are also excellent for smaller areas and trenches, delivering powerful impact to consolidate the clay.
Compaction is not strictly needed for every type of project, but it is essential for most construction projects involving soil as a foundation or structural component. Projects where undisturbed, naturally dense soil already provides sufficient bearing capacity and stability might not require engineered compaction. However, for most structures like buildings, roads, and embankments, compaction is critical to ensure stability, prevent settlement, and enhance load-bearing capacity.